Ever struggled with damper failures in extreme conditions? The secret lies in material selection and structural engineering.
Rotary damper reliability depends 80% on material-structure synergy. At Peir, we engineer application-specific solutions using advanced polymers and precision geometries for consistent performance.
During my 12 years at Peir, I've seen how material choices make or break damper performance. Let's explore why this technical synergy matters.
How Do Materials Impact Damper Performance?
Why does your medical equipment damper fail while industrial versions last? Material science holds the answer.
Medical-grade dampers require FDA-compliant POM for smooth operation, while automotive dampers need glass-filled nylon for heat resistance up to 120°C.
Consider these critical material factors:
-
Temperature Resistance:
- Standard nylon works for 0-80°C office equipment
- Glass-reinforced polymers handle 120°C automotive underhood conditions
- Special composites withstand -40°C to 150°C in aerospace applications
-
Chemical Compatibility:
- Hospital equipment needs sterilization-resistant materials
- Marine applications require saltwater-proof composites
- Food processing demands FDA-approved polymers
-
Wear Characteristics:
- PTFE-impregnated materials for high-cycle applications
- Self-lubricating composites for maintenance-free operation
- Metal-on-metal designs for extreme load scenarios
We recently solved a wallbed manufacturer's issue by switching from standard seal ring to fluororubber, increasing lifespan by 300%.
What Structural Designs Solve Real-World Problems?
Why do 43% of damper failures stem from improper structural integration? The devil's in the geometric details.
Peir's patented helical groove design ensures well damping performance in small activate angle across 30,000+ cycles, unlike conventional straight-groove dampers.
Let me share a case study from our Mexico facility:
Challenge: A car seat manufacturer needed consistent reclining resistance across different climates.
Solution: We developed:
- Dual-stage damping channels
- Temperature-compensating spring geometry
The result? 0.02Nm torque consistency from -30°C to 85°C. Here's what we consider in structural design:
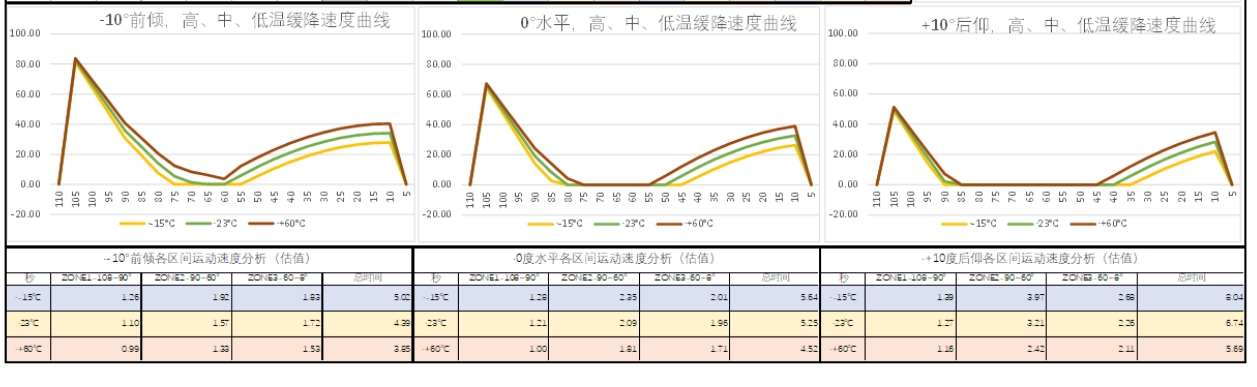
-
Load Distribution:
- Radial vs axial force requirements
- Moment arm calculations
- Bearing surface optimization
-
Environmental Factors:
- IP67 sealing for outdoor use
- Vibration-resistant mounting
- Corrosion-proof fasteners
-
Ergonomic Considerations:
- Soft-start mechanisms
- Adjustable damping profiles
- Noise reduction features
How Does Peir Customize Solutions?
Why trust generic dampers when your application needs precision engineering?
Our 5-step customization process analyzes your exact requirements - from CAD simulations to real-world prototyping - ensuring perfect damper integration.
Here's how we helped a Turkish elevator manufacturer:
-
Application Mapping:
- Door closing speed analysis
- Safety regulations review
- Maintenance cycle evaluation
-
Material Selection:
- Chose oil-retentive composite
- Added UV stabilizers
- Incorporated anti-static additives
-
Structural Optimization:
- Designed dual-rate damping
- Integrated position sensors
- Developed fail-safe mechanism
The customized solution reduced service calls by 60%. Our global engineering teams can help you with:
- Material Testing: ISO 527 tensile tests, DIN 53504 compression tests
- Simulation Services: ANSYS stress analysis, CFD modeling
- Prototyping: 3D printing, CNC machining
- Validation: 50,000+-cycle endurance testing
Conclusion
Ready to solve your damper challenges? Contact Peir's engineers today for application-specific solutions.