Creating high-performance dampers requires more than standard engineering - it demands a methodical approach tailored to real-world conditions. Many manufacturers skip critical validation steps, leading to field failures.
Peir Dampers follows a rigorously structured 8-phase design process that transforms application requirements into reliable damper solutions, incorporating simulation testing, prototyping, and full validation before production begins.
The comprehensive methodology ensures every damper meets exact operational needs. Let's examine each critical phase.
Why Does Application Study Matter in Damper Design?
Understanding real-world usage prevents product mismatch.
PeirDampers engineers begin by documenting installation environment forces loads motion patterns and lifecycle expectations ensuring the design matches actual operating conditions from the outset.
Key Application Study Factors
Focus Area | Data Collected | Design Impact |
---|---|---|
Motion Profile | RPM angular range cycle frequency | Torque curve optimization |
Environmental | Temperature humidity chemicals | Material selection |
Load Conditions | Static dynamic shock loads | Structural reinforcement needs |
Space Limits | Available cavity dimensions | Size/shape constraints |
Life Expectancy | Operational cycles per year | Durability requirements |
Clients provide usage details through a standardized questionnaire followed by engineering interviews.
How Does Concept Development Drive Innovation?
Multiple design options create solution flexibility.
The engineering team generates 3-5 concept proposals with varying performance characteristics cost points and installation approaches for client review before detailed design begins.
Typical Concept Variants
Concept Type | Advantages | Considerations |
---|---|---|
Standardized | Lower cost faster delivery | Limited customization |
Hybrid | Balance of cost performance | Moderate tooling modifications |
Full Custom | Perfect application match | Higher cost longer lead time |
Concept selection involves joint technical-commercial evaluation with the client.
What Role Does BOM Preparation Play?
Material selection directly impacts performance durability.
PeirDampers selects each component material based on mechanical properties environmental resistance and manufacturing considerations creating a complete inventory of all required items before CAD modeling.
Critical BOM Components
Element | Selection Criteria | Common Options |
---|---|---|
Housing | Strength temperature resistance | POM PP glass-filled nylon |
Shaft | Wear resistance precision | Stainless steel hardened alloys |
Seals | Friction chemical resistance | FKM NBR PTFE compounds |
Fluid | Viscosity temperature stability | Silicone oils hydrocarbon gels |
The BOM undergoes engineering and procurement review before finalization.
Why Is CAD Simulation Essential?
Virtual testing catches design flaws early.
Advanced FEA software analyzes stress distribution fluid dynamics and wear patterns allowing optimization before physical prototyping reducing development time by up to 40%.
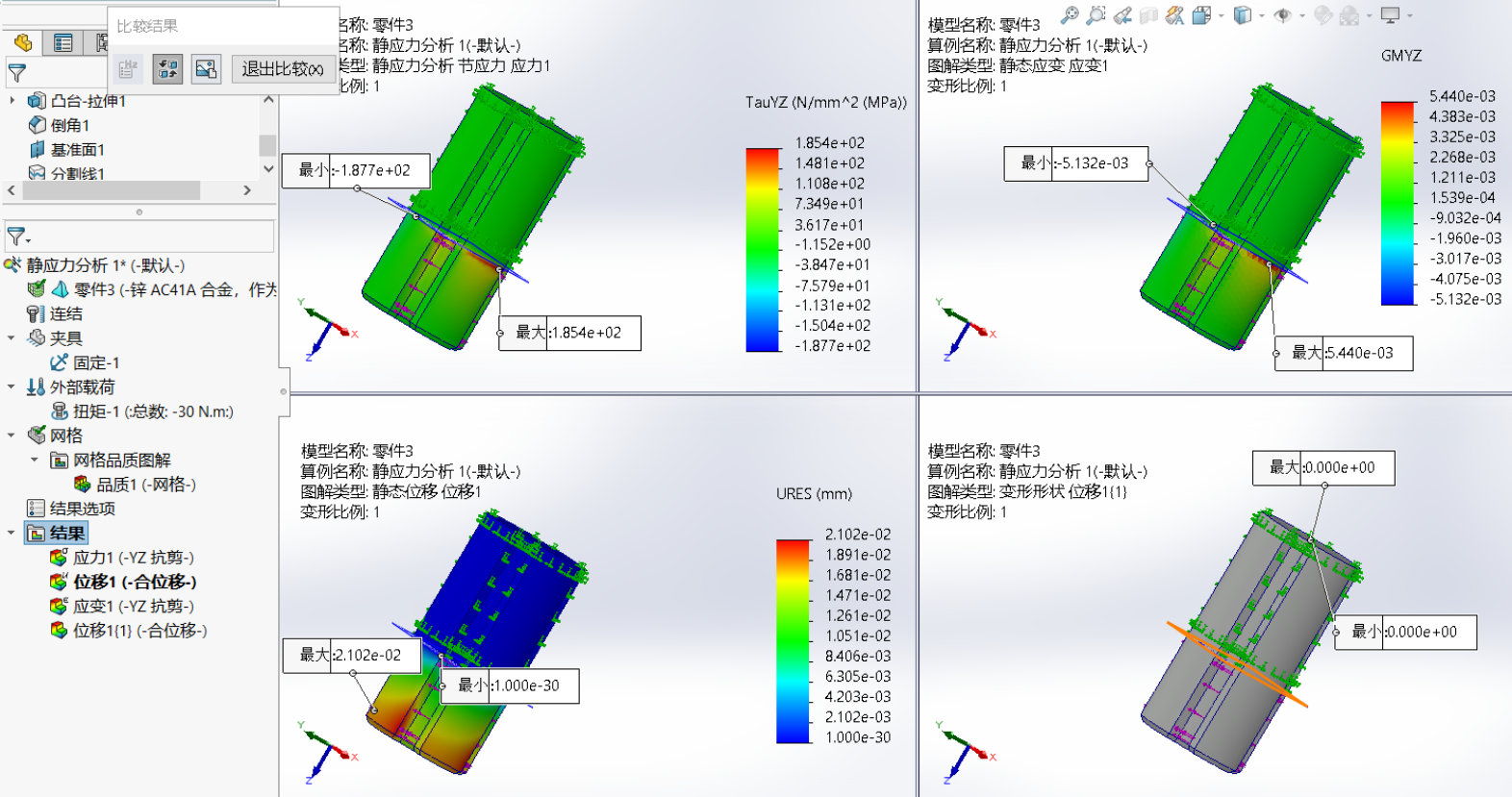
Simulation Parameters
Analysis Type | Key Outputs | Design Improvements |
---|---|---|
Structural | Stress concentration points | Wall thickness adjustments |
Fluid Dynamics | Pressure velocity profiles | Internal channel optimization |
Thermal | Heat distribution patterns | Material changes for hot spots |
Kinematic | Motion interference checks | Clearance modifications |
Simulation reports become part of the permanent product documentation.
How Do Prototypes Validate Designs?
Physical models prove real-world functionality.
Functional prototypes using 3D printing rapid tooling or machined components undergo laboratory and customer-site testing to verify performance meets specifications before production tooling begins.
Prototyping Methods
Technique | Advantages | Typical Use Cases |
---|---|---|
3D Printing | Fast turnaround low cost | Form factor verification |
CNC Machining | Precise material properties | Functional performance testing |
Soft Tooling | Near-production materials | Small batch field trials |
Prototypes are tested under both ideal and extreme operating conditions.
What Does Production Preparation Involve?
Transition to manufacturing requires careful planning.
Final design optimization focuses on manufacturability establishing quality control points and developing assembly procedures to ensure consistent mass production quality from the first batch.
Production Readiness Activities
Activity | Purpose | Output |
---|---|---|
Tooling Design | Create molds fixtures jigs | Production equipment |
Process Mapping | Define assembly steps | Work instructions |
QC Planning | Establish inspection points | Quality control documentation |
Pilot Run | Verify production capability | First article samples |
The complete process typically takes 8-12 weeks for new damper designs.
Conclusion
PeirDampers' systematic design methodology ensures every damper solution meets application requirements through rigorous analysis prototyping and validation ultimately delivering reliable long-lasting performance in real-world conditions.